Do you have an upcoming build involving large quantities of plywood sheets? That will present you with some challenges beyond what smaller projects face. A lot can go wrong once you transport plywood supplies, store them, or cut them into smaller custom pieces. And if you think you can handle plywood safely without expert help, you are in for a major headache.
To avoid any accidents or losses, here are a few tips on how you can safely manage plywood in bulk.
Safe Handling of Plywood Supplies
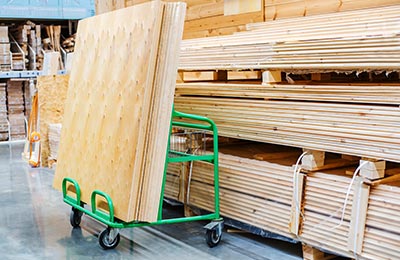
What makes plywood such a great material is that it comes in a variety of sizes or dimensions. Unfortunately, large sheet sizes can also pose challenges to safe handling and storage.
Tip #1. Proper stacking promotes safety.
Never underestimate the danger of sheet materials, no matter what they’re made of. And plywood is no exception to this rule.
When plywood supplies are improperly stacked or immobilised, it is an accident waiting to happen. Workers can get seriously injured if plywood sheets stacked on their edges suddenly shift and fall in their path.
Improper stacking and inadequate protection from the elements can also result in damages to the plywood material itself, especially its outer veneers. Plywood can fall off its storage place and sustain damage from serious impact or spills (i.e., chips, breaks, stains). It can also absorb or lose too much moisture, increasing its tendency to warp, expand or contract.
To preserve the plywood and maintain staff safety, you need:
- A well-chosen piling area. It should be sheltered from the elements and well-lit during work hours. It should also be within easy reach of anyone working at the construction site, for easy access.
- Adequate stacking surface(s). Use pallets, planks, and even leftover plywood wedges to form a platform that’s flat, firm, and lifted off the ground. It should be high enough from the ground or floor to protect the new plywood supplies from dirt or liquid spills, but low enough to avoid instability. Then you can safely stack your plywood sheet on these.
- Proper stacking method. As much as possible, avoid stacking the plywood on its edges, especially in large quantities. These are more stable when stacked flat. But don’t stack them too high or they will lean to one side; follow stacking height limitations. Place signs or markers on nearby walls or posts to remind everyone of the maximum height and other safety rules. You may also build the plywood stack in between other sturdy construction containers (e.g., large barrels or drums) to further prevent it from shifting. Cover the plywood with a sheet if necessary for extra protection.
Tip #2. Think carefully about when and how many sheets are moved and used.
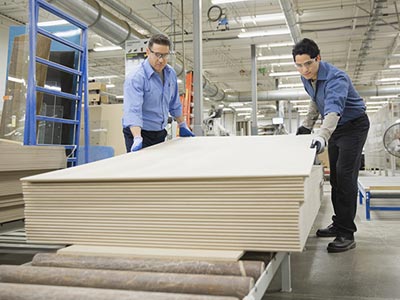
Transporting plywood sheets in bulk to your construction site or nearby storage facility should not be a problem. Your plywood wholesaler should be able to handle the delivery for an extra charge. But once there, you and your team must handle all that material yourselves.
A full-size plywood sheet often measures 2400 mm x 1200 mm (sometimes 2440 mm x 1220 mm) in width and length, which can be difficult for workers to handle or move around on-site. Moreover, depending on the wood source and sheet thickness (e.g., 19 mm), such a plywood sheet can easily weigh anywhere from 25 to 30 kilograms. Some heavier wood varieties (e.g., marine plywood and Baltic Birch) can add an extra 4 to 6 kilograms.
You might think that moving 25 kilograms should be quick, doable work for one or two people. But bear this is 25 kilograms of plywood, with unwieldy proportions. That makes it difficult to move each plywood sheet quickly through tight spaces, without getting the veneer damaged, knocking other things over, or injuring someone.
To manage the movement and use of plywood on your site, focus on:
- Sufficient manpower. To handle plywood sheets safely and effectively, be sure to have enough hands for the scale of the job. Don’t expect only a handful of staff to install plywood sheets within a day or two on a project meant for a dozen people, without accidents.
- Proper equipment and safety practices. Additionally, your personnel must be equipped with enough carts, hoisting equipment, and even lifts to handle the movement of plywood sheets throughout the job site. Everyone must follow appropriate construction safety precautions at all times (e.g., wear hardhats, safety goggles, masks, respirators).
- Orchestrated movement of material. For large and complex constructions, a strict schedule is a plus. Specify specific dates and time slots for how much of the plywood is moved into its final place and installed. You have better control over operations this way and lower the possibility of accidents when different team operations overlap.
Tip #3. Minimise in-house plywood cutting to lower risks.
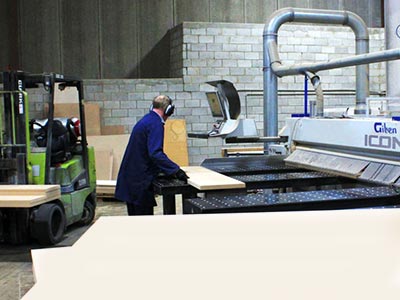
Sawing a sheet of plywood by yourself can already be dangerous. Imagine having this risk multiplied by the number of plywood sheets your personnel must install in your project.
There are many different grades for plywood. Do you have the right mechanised blade and tools for the plywood you’re working with? Do you have sufficient workspace for that operation? How skilled and experienced are your people? All these will determine the level of risk in your construction.
And it’s not just an issue of possible physical injuries among construction workers. The more woodworking is done at a job site, the higher the amount of wood dust is in the air.
Cutting up plywood sheets and planks in large numbers generates wood dust. While this is finer than sawdust from timber cutting, it is just as flammable.
Wood dust is also even more of a health hazard. Repeated exposure to it can cause eye and nose irritation, rhinitis and other allergic reactions, nose bleeds, skin disorders, asthma attacks, and even minor damage to lungs and cancer.
To avoid these problems, here are the best practices you should adopt:
- A dust remediation system. If heavy reworking of plywood is needed, employ the use of dust and fumes extractors on-site, to keep the level of wood dust down.
- Maximum eye and lung protection. Wearing special masks and protective goggles should be strictly enforced. This offers you and your staff maximum protection from inhaling dust and experiencing respiratory issues.
- Pre-cut plywood. Pay for a professional plywood cutting service to do most or all of the plywood pre-cutting for you. Your plywood wholesaler should have such a service; they have more experienced professional personnel and specialised equipment to do the job before the supplies are delivered to you. That will reduce the amount of work your team needs to do.
Consult experts on safe plywood handling practices
Before anything else, it’s best to consult plywood experts or plywood suppliers in your area. You may think that not all these safety measures are necessary for your particular build. But it is better to keep safe than be sorry. One accident can derail an entire project or business.
FA Mitchell can provide you with all the expertise you need. Apart from supplying a wide range of plywoods, MDFs and particleboards, we also provide relevant expert services to assist you with your projects. We can help shorten project operations by cutting your plywood, particle boards and MDF wood panels to size, and delivering these straight to whichever site you wish.
The knowledgeable staff at FA Mitchell have many decades of experience on how to handle plywood safely. Use our expertise and advice, and save yourself from paying too much or ending up with substandard products.
Call us now so we can assist you. We’re eager to help you complete your project, no matter where you are in Australia.