Years ago, plywood in floors was limited to sheathing and underlays. Nowadays, it’s utilised as a cost-effective flooring finish as well. Thanks to technological improvements, plywood flooring is now a viable alternative to most other floors. It offers a durable and more affordable solution for many construction projects.
But before you consider using plywood flooring in your project, here are the most important things you must know.
What makes plywood flooring durable?
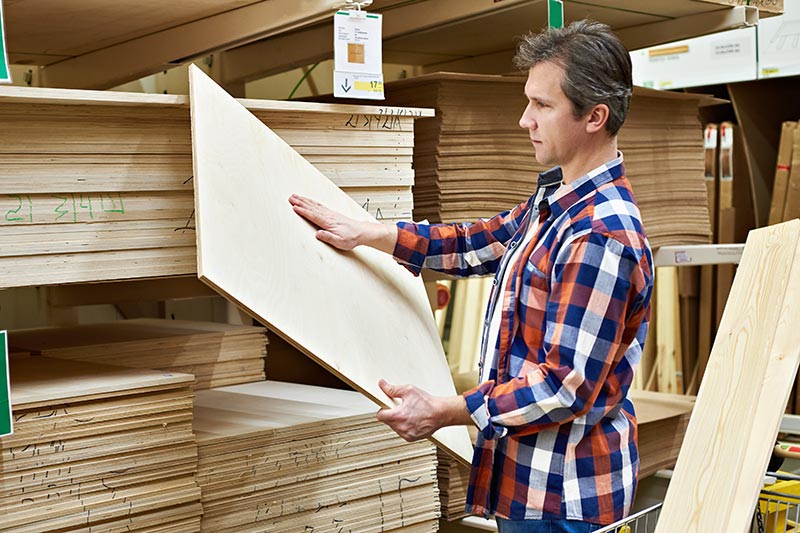
Plywood is a composite building material. It’s made of several thin sheets of wood veneer or “plies.” These are produced by a machine that rotates harvested wood logs and peels them off.
Each veneer sheet or ply is first rotated to a different angle before bonded to another sheet with strong adhesive. Then it’s all compressed under heat into a much denser material.
That method creates what’s called “cross-graining.” By compressing veneers in different angles, plywood manufacturers can reinforce the material with wood grains that run perpendicular to one another. This reduces the plywood’s tendency to split, warp, expand, or contract.
Moreover, plywood manufacturers often use better-quality veneers for the outer layers. The lower-quality inner layers create a separation between the outer layers on each side of the panel. If any stress strikes one outer layer, less of the force gets transferred to the other side. This makes plywood even more resistant to bending.
All these characteristics make plywood durable and flexible enough for either structural applications or as a decorative finish.
This is also why it makes an excellent alternative to expensive hardwood floors.
How to use plywood in floors
You can use plywood to create a significant portion of a floor system.
As a subfloor
Plywood for subflooring usually comes in interlocking sheets (i.e., with interlocking tongues and grooves). When installed directly on top of the joists of a floor’s framing system, it forms a secure base for the finished floor layer that will be laid on top of it.
A plywood subfloor can support many types of floor finishes or coverings, including carpet, laminates, bamboo, and hardwood.
As underlayment
Depending on what kind of floor you’re creating, you may need an underlayment on top of the subfloor. This optional layer provides a stiffer, smoother surface for the final top layer to rest on. It can also act as an extra moisture or sound barrier. For this, you can use plywood as well.
As a finished flooring
You can install plywood as the finish or “covering” on top of an existing subfloor. (And yes, you can have plywood flooring over a plywood subfloor.)
You can cut plywood into planks or special shapes and lay them in whatever pattern you prefer. Some plywood flooring designs even mimic traditional wood parquet floors or mosaics.
Current examples
To experience how a plywood floor can look and feel, go find the latest examples in the following places:
- Hotels and motels
- Offices
- Restaurants or cafés
- Garages
- Decks
- Spas and beauty salons
- Yoga studios
- Music and recording studios
Characteristics of the best plywoods for floors
But first, consider what sort of physical movements, weight loads, and environmental conditions your particular floor will have to endure. Aside from varying levels of thickness, there are also many types and grades of plywood for different applications. Not all of them may be appropriate to your project.
So when you’re shopping for plywood flooring in Australia, here’s what you should look for.
1. The EWPAA stamp
In Australia, the best plywoods for floors follow the Australian Standard AS/NZS 2269 for plywood. The Engineered Wood Products Association of Australasia (EWPAA) audits its accredited member-manufacturers and compels them to place the EWPAA stamp on every plywood sheet they produce. This lets consumers know that their product complies with that Australian standard.
So make sure that the plywood you’re getting has that EWPAA stamp. Each panel should also bear the plywood mill’s code, construction specifications, bond type, and stress rating. (More on these below.)
2. Better cross-graining
When you can, ask a plywood manufacturer for details on how they set the cross-graining in their products. Some manufacturers set the plies only at right angles to one another.
For floors, look for better-quality plywood plies angled in steps of 45 degrees (e.g., 45, 90, 135, etc.). This gives the plywood better strength.
3. Higher quality bonding
There are four types of resin adhesive or glue bonds that EWPAA-audited mills use when manufacturing plywood.
Type A – This is a phenol-formaldehyde resin used to create the most durable plywoods. These can withstand heat, cold, and wet conditions. This is used for marine and exterior plywoods.
Type B – This melamine-fortified resin isn’t as strong as Type A, but it creates plywood durable enough for exteriors. Some structural plywoods have either Type A or B bonding and can be used for concrete formwork.
Type C and D – These are weaker urea-formaldehyde resins. Manufacturers use them to create plywoods for interior applications. These plywoods cannot bear heavy weights or stresses and should not be used in structural applications.
For plywood floorings, subfloors, and underlays, you should consider only Types A or B. (This will also depend on what your construction project requires.)
4. Higher stress rating
Floor plywoods should also have a sufficiently high stress rating or grade.
The EWPAA conducts tests to determine how much strength and stiffness a particular manufacturer’s product has. There’s an established grading system for this. The plywoods that are best-suited to floors are those with stress grades of F7 to F34. (See more info about structural plywood and appropriate stress grades in the latter sections of this page.)
5. Preservative treatment
Where are you installing your plywood floor? If it’s going to be exposed to the weather and other destructive elements (e.g., termites, fungi), choose a plywood that’s been treated or subjected to a preservative.
Here are some examples of how plywood is treated to prevent decay:
- Prior to production, preservatives are infused into the veneers
- Plywood is given extra pressure treatment
- A hard top preservative coating is applied over the surface after production
6. Appearance grades
Plywood also has a separate grading for the finish or appearance of its outer veneers:
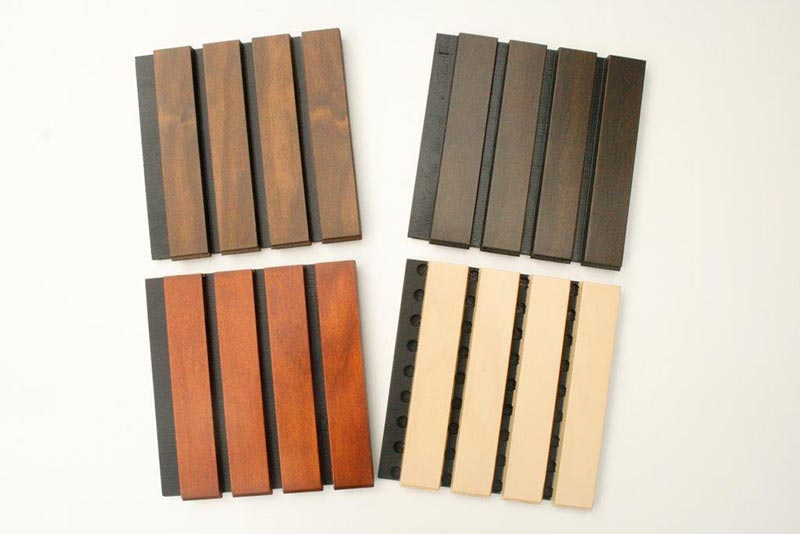
Grade A – This is the highest rating. It means the quality of the plywood’s outer or face veneer finish is smooth and attractive. If you want a plywood flooring with a clear finish, get plywood with this grading.
Grade S – In this grade, the outer veneer shows off more of the natural characteristics of the wood. But it’s still decorative enough for use in clear finishes.
Grade B – Plywood of this veneer grade is suitable for high-quality paint finishing, such as what you would need for walls or even certain floorings. You may find knots, minor holes, or filled splits on this material’s surface.
Grades C and D – Plywoods with these grades have many visible imperfections or defects on their outer veneers. These are usually used for structural purposes (e.g., plywood bracing). For floors, this is the veneer grading that plywood for subfloors and underlays often have.
Note: Each side of a plywood sheet gets a “veneer grade” of its own. So you will find plywood sheets that come with appearance grades like AA, AB, SB, BB, CC, AC, AD, CD, and so forth.
Plywood application types for floors
Searching through the different plywood ratings or grades can be confusing for consumers. So to simplify their search, suppliers and retailers like to categorize and sell plywood according to use.
The best types of plywood for floors often come under these labels:
1. Structural plywood
Structural plywood is primarily for the internal structures of buildings and homes (e.g., roofs, bracing of timber frames for interior walls, floor sheathing or subfloor).
While it’s usually made from hardwood tree species, there are softwood versions as well. The plies are manufactured with an extra-strong phenolic adhesive. So the resulting plywood has a better load-bearing capacity, thermal insulation, and resistance to heavy blows than other types. Structural plywood is also versatile enough for both internal and external plywood cladding (especially if treated with a preservative to prevent decay).
You could even use this to create most of the floor system of a room or space, from subfloor to flooring. Structural plywood is often not for show, however. Unless you specify with the supplier that you’re looking for a great veneer grade on one side (to be used as finished flooring), you’ll end up with structural plywood that’s meant to be used but not seen.
Typical plywood ratings and qualities:
- Type A bond
- Common stress ratings of F8 to F14 (and sometimes higher)
- Non-corrosive and treated for resistance to moisture, biological rot, certain chemicals, and even fire
- Veneer grades are often combinations of C or D (e.g., CC, CD, DD). But some can have grades like AD or BD (for structural plywood with one side left exposed in certain architectural designs).
2. Exterior plywood
This type of plywood is for places or situations that need a high-quality, aesthetically pleasing finish, and have less of the structural or load-bearing requirements. You’ll find this type often in interior walls and non-structural claddings. It’s decorative enough for a clear finish.
When it comes to floors, exterior plywood can and should only be used as finished flooring in relatively low traffic or light weight-bearing interiors (e.g., a hotel guest room).
Typical plywood ratings and qualities:
- Type A or B bond
- Common stress ratings of F7 to F14
- Should have some treatment to prevent fungal growths; might also be fire retardant
- Veneer grades: a higher-quality face on one side (A, B, or S) and lower quality on the other (C or D).
3. Marine plywood
Marine plywood is among the most expensive of plywoods. It combines the load-bearing properties of structural plywood and the beauty of exterior plywood. It’s waterproof and made out of the finest water-resistant tropical hardwood.
It’s often used in boat hulls and other marine applications, but it can also be used for other construction projects with similar requirements. If you need a floor that can withstand heavy loads, stress, moisture, and condensation (e.g., garden deck, gazebo floor, boat deck), marine plywood is the perfect material for you.
You can paint, varnish, or gloss it, or just give it a plain clear finish.
Typical plywood ratings and qualities:
- Permanent Type A bond
- Superior stress ratings of F14 to F34
- Waterproofed
- Should also have extra treatment to prevent fungal growths, insect infestations, and marine pests
- Might also be fire retardant
- Veneer grade: AA
The pros and cons of plywood flooring
Plywood generally provides several benefits for people who need a more cost-effective solution. However, when it specifically comes to creating floors, there are a few disadvantages and advantages you’ll have to bear in mind.
Disadvantages
Plywood provides several benefits especially for people looking for a more cost-effective solution. The material is also easy to handle and readily available in supply stores.
1. It’s prone to scratching or splintering.
Plywood’s unique production process helps make it more resistant to bending, warping, or expansion. However, it also results in a softer surface. That means plywood is still more prone to getting dented or chipped than hardwood or stone.
It’s a bit of a challenge to keep plywood floors looking pristine over the years. If a mishap occurs (like heavy furniture being moved), you’ll get a visible indentation or mark on the floor.
2. It won’t last a lifetime.
As far as engineered wood products are concerned, plywood sheeting is as tough as they come. It’s more durable than medium density fibreboards (MDF) and particle boards.
However, plywood can’t beat natural bamboo, premium hardwood, or hard stone (like sandstone, marble, or granite) in strength and durability. Not even the latest engineered hardwood or bamboo plywood comes close. After several decades, any waterproofing or anti-fungal properties plywood has will give way to decay, and replacements will be needed.
Advantages
1. It’s affordable.
One of the main selling points of plywood floors is their affordability. Adding flooring to your building can rack up a huge bill, especially with big construction projects. The larger the floor area you need to cover, the more you’ll have to spend on it. This is where plywood can come in handy.
A plywood floor won’t cost you as much to install as other materials (such as concrete or natural wood). Yet it can still provide the same beautiful finish as hardwood.
2. It’s durable.
Plywood may only be engineered wood. But thanks to the latest production technology it can be far more durable than you expect.
3. It’s readily available.
Given the right choice and execution, a plywood floor can look and feel as luxurious as any floor made of precious or rare materials. But unlike rare marble quarried from Italy or an expensive hardwood from a distant tropical country, plywood is always available at your nearest store or supplier. This is especially true of plywood made from locally sourced lumber (e.g., Australian Hoop Pine, Australian eucalypt hardwood).
4. It’s easy to handle and install.
Plywood is “predictable.” It’s engineered, it comes in uniform sizes, and it is heavily regulated. You’ll find it easier to purchase, transport, and store compared to other construction materials.
It also doesn’t take much to install plywood in a floor system. You can simply cut the sheet into your desired sizes. You can put the panels into place (thanks to interlocking tongues and grooves), then either nail or glue them down just as easily.
5. It’s easy to finish and repair.
Your construction employees will appreciate the flexibility of plywood as a construction material. You can have them paint and repaint plywood as many times as you wish. You can also have it stained for a more distinct look.
Yes, it’s prone to scratching, chipping, or denting. But you will find that plywood floors are also easier to repair compared to floors made of other materials. If you have any weathered portions, you can simply remove the damaged part and replace it with new plywood.
Choosing the right plywood flooring
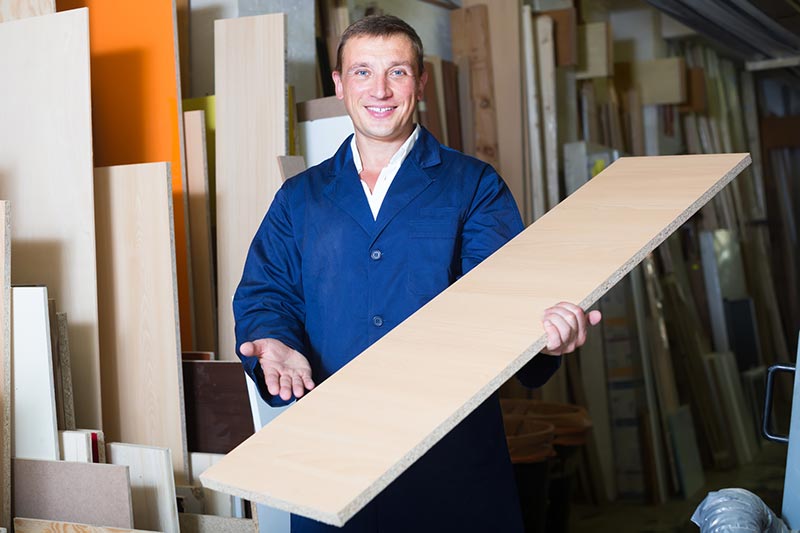
So which one of these plywoods is best for you? Do you really need to stick to Type A bonding or can you get away with using Type B, to save on costs? And which stress grade should you go with?
It all depends on the needs of your particular construction project. Unless you’re an expert, do consult an architect and a reputable plywood supplier to help pick out the right plywoods for your floor. Plywood may be cost-effective, but any mistakes in your choice of material will be costly in terms of replacements and repairs – so beware!
Need an expert plywood flooring supplier you can trust?
Do you need commercial quantities of plywood for your floor? FA Mitchell is here to help. Contact us today and we’ll be happy to assist you! We can advise you on the best types of plywood sheeting according to the particular purpose you have for your particular project.