Plywood can be a sustainable building material. But that’s only if it is produced, transported and used in safe and sustainable ways. So when you source plywood for your project, a question to always ask is: “How sustainable is this plywood?”
In addition, you want to ask yourself, “How do I choose and use plywood in a way that makes it more sustainable?”
To answer both questions, you need to first know plywood’s environmental impact during the main stages of its life cycle, from start to finish.
The 5 Main Areas of Environmental Impact
There are five stages in the life cycle of plywood. And the less negative impact a plywood make has on the environment across all these stages, the more sustainable it is.
1. Sourcing
The life cycle of commercial plywood begins with the acquisition of raw materials. Commercial plywood is primarily made from thin layers of wood veneer, typically sourced from different tree species like pine, fir, or hardwoods.
Acquiring raw timber for veneers means logging or harvesting trees. These are now often taken from commercial tree farms, which are a more sustainable forestry practice that still fulfils the worldwide demand for plywood. Done responsibly, this helps keep more of the world’s wild forests intact.
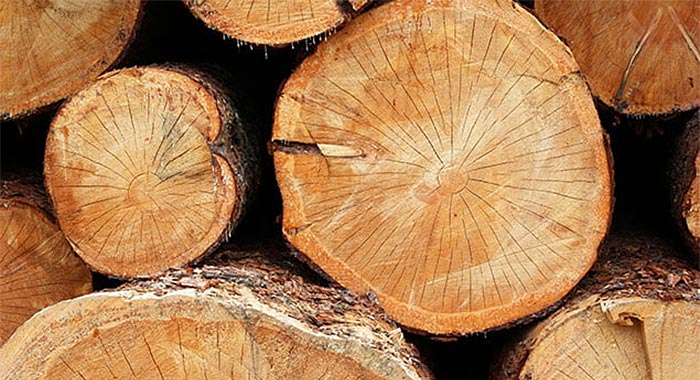
Sourcing issues that make plywood less sustainable:
1. Unsustainable woods. These are the expensive or endangered woods(e.g., certain types of mahogany, rosewoods or sandalwoods). Companies sometimes source these from wild forests that are critical to the planet’s carbon sequestration. Unsustainable practices like that lead to topsoil degradation, habitat destruction (both on land and in nearby bodies of water), biodiversity loss, and accelerated climate change.
2. Questionable raw timber sources. Some areas in the world have a reputation for poor forestry management and implementation of environmental protection laws. Even when plywood is made from more common materials (e.g. birch, pine, oak, mahogany, teak), if it’s sourced from these places at prices cheaper than that of their competitors, be cautious. There’s a chance that the raw timber is sourced illegally, through severe deforestation. It may even involve unjust labour practices and human rights abuses (more on that later).
You may personally associate such issues with evergreen and tropical forests abroad. However, remember that there can also be badly-managed timber operations within Australia. Such operations can destroy habitats for Australia’s unique and endangered species.
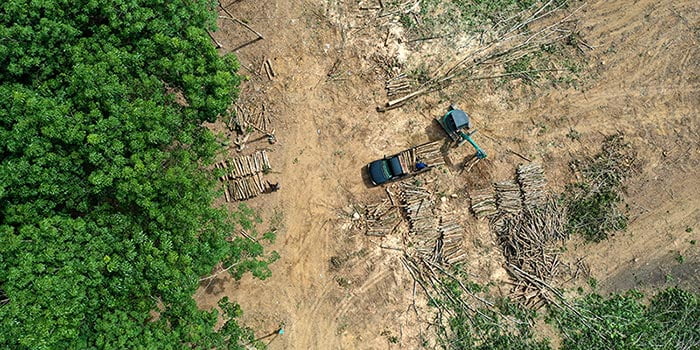
How to pick more sustainable plywood with fewer sourcing issues:
Look for plywood dealers that deal only with suppliers who can guarantee their wood material is produced through fair and sustainable practices. Ideally, their products should also have certifications or recognition from international pro-sustainability organizations (e.g., the Forest Stewardship Council). In this way, you support responsible timber sourcing, ecosystem conservation, and respect for local communities’ rights (again, more on that later).
You can also opt for alternative plywood material such as bamboo. Certain species of bamboo have long been used as strong and reliable building materials in Asia. Because this species of grass grows rapidly, bamboo plywood can easily be sustainable.
2. Manufacturing
The plywood industry creates the biggest impact on the environment during manufacturing.
Raw timber logs are first stripped of outer bark and soaked in hot water, then rotary cut into thin layers of wood called veneers. Once properly dried, the veneers are layered together and bonded with adhesives, under high temperatures and pressure. The resulting plywood panels are trimmed and sanded to achieve uniform thickness and smoothness.
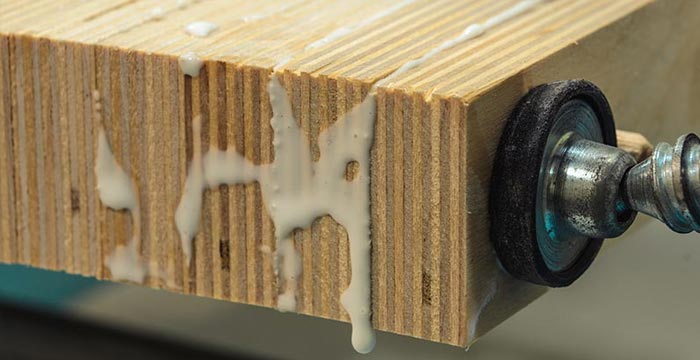
Manufacturing issues that can compromise plywood sustainability:
1. Adhesives with excessive VOC (Volatile Organic Compounds). Plywood often comes under scrutiny because of the adhesive resins used to glue its veneers together. While these resins have become easier and cheaper to produce and use, many still contain formaldehyde. Even after the manufacturing process is finished, the adhesives can still slowly release formaldehyde over time. If the outer phenolic coating or the resin bonds break down due to heat and moisture, the gas easily permeates the plywood veneers and goes straight into the surrounding air (indoors or outdoors). Prolonged or elevated exposure to formaldehyde has triggered unpleasant reactions (i.e., watery eyes, nausea, burning sensations in the throat) and difficulties in breathing (i.e., asthma) among some people. It is also carcinogenic.
2. Poorly-managed manufacturing conditions. Aside from VOCs released upon the application of veneer adhesives, the plywood production process naturally produces other by-products, which need to be dealt with. These include:
- Various organics (e.g. tannins, urea) associated with the storage, soaking, drying, and preparation of raw timber
- Wood particulates or wood dust from cutting veneers from logs and trimming finished panels
- Hydrocarbon or other chemical emissions from machines and power generators
If these are not effectively used or prevented from spreading into the air and neighbouring areas (e.g., forests, farmlands, rivers, coastlines, urban areas), these can become soil, air and water pollutants. These threaten the health of the industry’s workers, nearby natural habitats and communities.
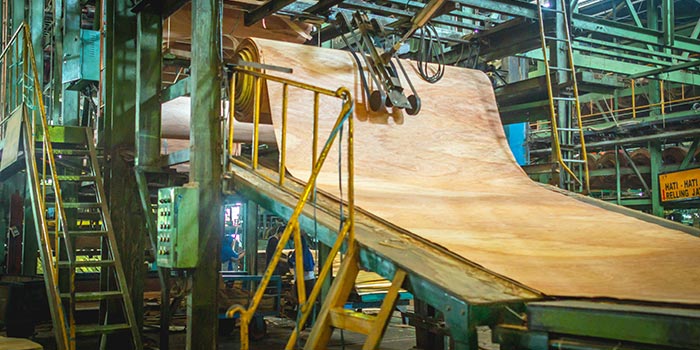
How you can support the manufacture of sustainable plywood:
- Formaldehyde-based resin adhesives are still common throughout the global plywood industry. However, plywood that passes the strictest and highest standards of industry regulators is considered low-formaldehyde emission building materials. By buying only high-quality low-emission plywood, you can be sure that emissions are negligible to non-existent. Insist on getting only plywood that has been properly audited by industry regulators (e.g., the Engineered Wood Products Association of Australasia or EWPAA).
- Whenever it is applicable or necessary, you may also opt for plywood that uses non-formaldehyde or non-toxic gluing systems. While they are relatively new on the market and more expensive (for now) compared to traditional plywood, these “greener” or environmentally friendly products could one day dominate the future plywood manufacturing industry.
- Deal only with suppliers that sell plywood with proper documentation. Each plywood brand should have stamps or certifications of its quality on its veneer face. There should also be data sheets provided for each plywood brand and type; ideally, these should indicate the type of wood used, where these were sourced, the mill of origin, construction specifications, bond or adhesive type used, stress rating, safety and hazard identifications, etc. Proper documentation is your proof that the plywood has been produced according to Australian Standard As/NZS 2269 and is therefore sustainable.
3. Transport
Transporting materials can occur at any point in the plywood life cycle. Nevertheless, it most often occurs right before and after the manufacture of plywood.
Depending on the location of the original timber source, moving materials can involve a wide range of distances and transport methods.
Some plywood markets are fortunate. Their sawmills, plywood manufacturing sites, storage warehouses, dealers (wholesale or retail), and various consumers are all located within one state or country. These minimize the amount of transport work needed to move plywood.
But more often than not, timber logs, veneers, adhesives, and finished plywood sheets must travel long distances – even across continents – via container ship, freight train or cargo truck, to reach various suppliers, construction sites, and individual users.
Consequences of excessive transport:
1. Increased carbon footprint. Transporting plywood materials becomes a great source of carbon emissions when these must be brought across great distances. Most bulk transportation of goods still relies on fossil fuel-powered vehicles (e.g., hauling vehicles or cargo trucks).
2. Packaging waste. Plywood is often transported as stacks of about fifty panels or more (secured with metal bands), without any special covering. But sometimes there will be conditions where they must be enfolded in large plastic sheets, secured within a wooden frame, and given extra padding in corners. Once the plywood is used, all these special covers, frames and padding become packaging waste. If these are used inefficiently and discarded or reused improperly, that can only contribute to the level of industrial global waste (biodegradables and plastics).
How you can encourage more sustainable transportation of plywood:
- It’s mainly an issue of localisation versus importation. Whenever possible, use plywood that has been sourced and manufactured within your country or region (e.g., plywood made from Australian Hoop Pine and Australian eucalypt hardwoods). Encourage your colleagues, neighbours, friends and family to do the same.
- Buy only from reputable dealers who sell plywood from sustainable suppliers, especially local or regional ones.
- Plan your construction projects and plywood orders carefully, to minimise the cost and impact of transport. Avoid scheduling multiple orders if you can have one bulk delivery.
4. Application or usage
Plywood has long been regarded as a versatile material, due to its strength, durability, and ease of use. Not surprisingly, it has a wide range of applications, such as furniture manufacturing, interior and exterior construction, packaging, and more.
When sourced and used responsibly, plywood is more sustainable than lumber.
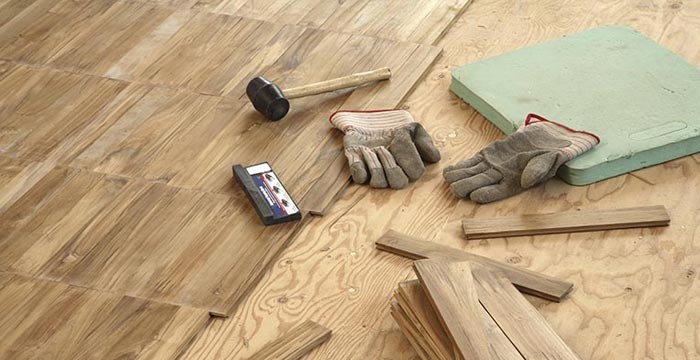
How to maximise the sustainability of your plywood:
- Choose your plywood with care. Use the best type of plywood for the job required (e.g., structural plywood for subflooring, marine plywood for outdoor or high-moisture areas). Do not cut costs by getting lighter or cheaper plywood for applications that require weatherproof or weight-bearing material.
- Make sure your construction architectural plan and interior design provide enough ventilation and extra protection for any plywood use.
- Before and during installation, make sure your plywood is protected from too much moisture, heat, and dust. Aside from helping any VOCs permeate into the wood veneers, these elements can also turn the plywood into an attractive home for termites, wood borers, and various harmful moulds.
- If your project is located in an area prone to bushfire or termite infestations, get plywood that’s fire-resistant or has been specially treated to discourage termites.
- Years after installation, have periodic maintenance checks made. Have the plywood treated for termites or wood rot if needed.
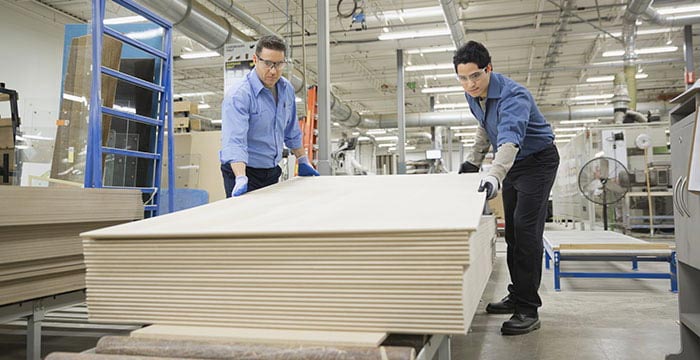
5. End-of-life or reuse
Compared to more expensive natural hardwood lumber, plywood has a low-to-medium life span (usually no more than 20 years). It is more prone to damage or warping, especially after several years to a decade have passed since its installation.
And once damaged, plywood is often discarded and replaced. Old plywood isn’t strong enough for many construction purposes, so the possibilities for reusing it are limited.
Issues with discarded plywood:
1. Air pollution from burning or incinerating plywood for fuel. Unlike pure wood, when plywood is incinerated it doesn’t just yield carbon and organic ash. The volatile organic compounds (VOCs) in the adhesives will also be heated, which releases toxic fumes into the air.
2. Problems stemming from waste accumulation. Plywood veneers are biodegradable. However, in large quantities, their lamination and adhesives can become toxic soil pollutants. This can happen whether the used plywood is piled up whole, ground into bits, or buried underground. VOCs make large quantities of plywood (and similarly treated wood) unsuitable for composting. Moreover, in certain parts of the world (especially in Australia), piles of used plywood can also become a breeding ground for pests or dangerous wildlife.
How to reuse or recycle old plywood for reduced environmental impact:
- Even when old or damaged, some types of all-weather plywood can still be reused or recycled to make simple furniture (e.g., stools or side tables), decorative art (e.g., painting frames), and non-essential exterior cladding for decorative garden or playground features (e.g., planter boxes; benches in a gazebo; decorative mulch).
- For other types of plywood that are too weak or damaged for reuse, instead of selling them to a junk dealer or burying them in a landfill, you can divert them to your nearest waste-to-energy plant. (In Australia, try looking up the Kwinana Waste to Energy Project by the Australian Renewable Energy Agency / ARENA.)
- Another option is to resell old plywood to local particleboard manufacturers who can shred and use it as material for their products.
The Human Cost
When assessing the sustainability of plywood, don’t stop at environmental costs. You should also consider the possible impact on human beings, especially those from marginalised communities.
The most common plywood industry-related issues that negatively affect human communities the most (and which ultimately lower the sustainability of the plywood itself) are:
- Occupational Health and Safety: Without proper implementation of laws, monitoring, and advocacy, the sourcing and manufacturing stages of plywood can involve hazardous and questionable working conditions for workers. Anything from extreme weather conditions and harmful chemicals to low wages and human rights abuses is possible. This is especially in states or countries plagued by poverty, corrupt politics, and economic dependence on more developed nations.
- Unjust use of forests and tribal lands. Some logs for plywood veneers may have been harvested from wild forests or “legalised” agricultural development areas that (in reality) were seized or unjustly wrangled away from indigenous peoples, ethnic minorities, or marginalised communities who relied on natural ecosystems for food, shelter, income, or cultural heritage. Such communities often bear the brunt of environmental impact due to plywood production (i.e., pollution, deforestation, and land degradation). That undermines their livelihoods and cultural practices and exacerbates existing social inequalities.
All these problems usually come in tandem with the same negative practices that are unsustainable and destructive towards the environment.
Thus, if you seek the same environmentally-responsible plywood brands, chances are they will also be into fair trade and labour practices.
Promoting plywood sustainability
To promote plywood sustainability, you need to support the right plywood brands. These are from companies that implement responsible sourcing practices, develop non-toxic and energy-efficient manufacturing methods, improve waste management, encourage recycling and reuse, and safeguard the rights and well-being of every community that the whole process touches.
Of course, that’s going to be a challenge. Most of the world’s plywood comes from no more than 15 countries (e.g., China, India, the United States, Indonesia, Brazil, Vietnam, Malaysia, and Canada), and not all of them have the same standards of sustainability in timber harvesting, manufacture, and distribution can vary between them. But ultimately, the cumulative efforts of consumers like yourself should drive everyone toward the evolution of greener and more sustainable plywood.
If you need advice on what sustainable plywood you can use for your project, contact FA Mitchell today Our in-house experts know sustainable plywood well and we sell only the products that have been manufactured according to Australian Standard As/NZS 2269 and audited by the Engineered Wood Products Association of Australasia (EWPAA).
Extra references:
- Kilvert, Nick. “Timber Can Be More Sustainable Than Other Building Materials, But It Comes With Some Caveats – ABC News.” ABC (Australian Broadcasting Corporation), ABC News, 24 Jan. 2019, https://www.abc.net.au/news/science/2019-01-24/timber-can-be-more-sustainable-than-other-building-materials/10736496.
- “Which Country Produces the Most Plywood? | Helgi Library.” Helgi Library, https://www.helgilibrary.com/charts/which-country-produces-the-most-plywood/. Accessed 22 June 2023.
- “Kwinana Waste to Energy Project – Australian Renewable Energy Agency (ARENA).” Australian Renewable Energy Agency, https://www.facebook.com/AustRenewableEnergyAgency/, https://arena.gov.au/projects/kwinana-waste-to-energy-project/. Accessed 22 June 2023.